IC Baking and Dry Packing
IC Baking
- Baking performed in high-accuracy, temperature and humidity controlled environmental chamber.
- Capacity to bake and dry pack up to 5,000 chips in 3 days (size dependent).
- Support for all package types and all moisture sensitivity levels.
- All baked chips are sealed with desiccant and moisture level indicator cards.
Why is IC Baking Necessary?
The major concern with moisture sensitive parts is that the plastic packaging around the part will absorb water (typically from the air.) When it comes time to assemble a circuit board and the part undergoes reflow soldering, the moisture in the packaging can have very destructive effects. Due to the high temperature of the reflow process, the water absorbed by the part boils. The boiling causes bubbles to form inside of the plastic packaging. The force of these bubbles (the force of the expanding water) deforms the part and often damages the internal components. The visible damage done to the part is called “popcorning.”
Moisture sensitivity of a particular integrated circuit is defined by its Moisture Sensitivity Level. The higher the Moisture Sensitivity Level, the more rapidly the part will absorb water. These levels range from MSL 1 (which can be left in the open indefinitely and will not absorb any moisture) to MSL 6. MSL 6 parts can only be left out for 6 hours before baking is required.
Baking integrated circuits allows the water to evaporate gradually and completely. This ensures that when the parts are soldered there is almost zero moisture in the packages and the risk of part damage (or “popcorning”) is eliminated. There are various methods of baking – which method to use is dependent upon the nature of the part and the required timeline of the job. Parts can be baked at low temperature (40 degrees Celsius) in an ultra-low humidity environment for a long period of time (usually 9 to 30 days dependent upon part type and thickness.) Alternatively, they can be baked at 125 degrees Celsius for a much shorter time (usually between 5 and 48 hours.) Each of these methods ensures that any moisture within the chip evaporates in a controlled manner – no chip damage occurs during the baking process.
Once ICs have been successfully baked, APS immediately dry packs them with desiccant and a moisture level indicator card to ensure successful problem-free soldering. It is very unlikely that during normal production operation any IC will undergo the sort of rapid heating experienced during reflow soldering. Once the part has been soldered to the PCB you can be confident that moisture sensitivity is no longer a concern.
Tape and Reel Service available for most baked parts.
We follow the IPC/JEDEC J-STD-033B.1 Standard for baking procedures.
Dry Packing
According to the Moisture Sensitive Level of the device, this determines if the devices need to be Dry Packed. Please see Moisture Sensitive Levels below:
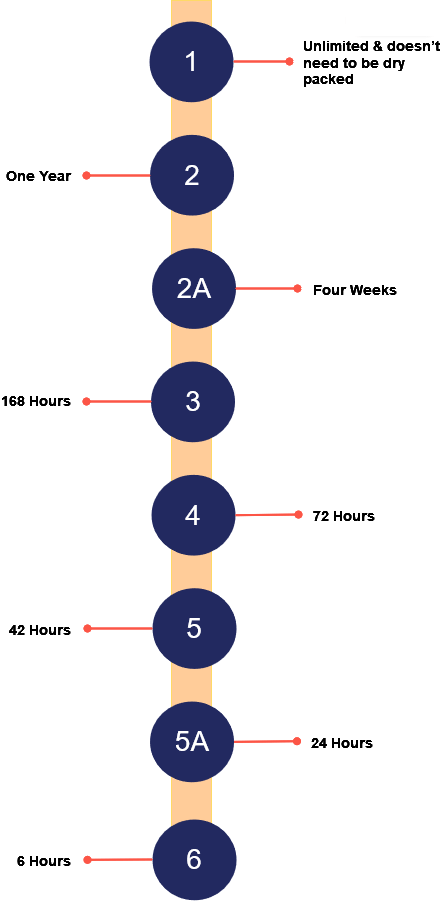